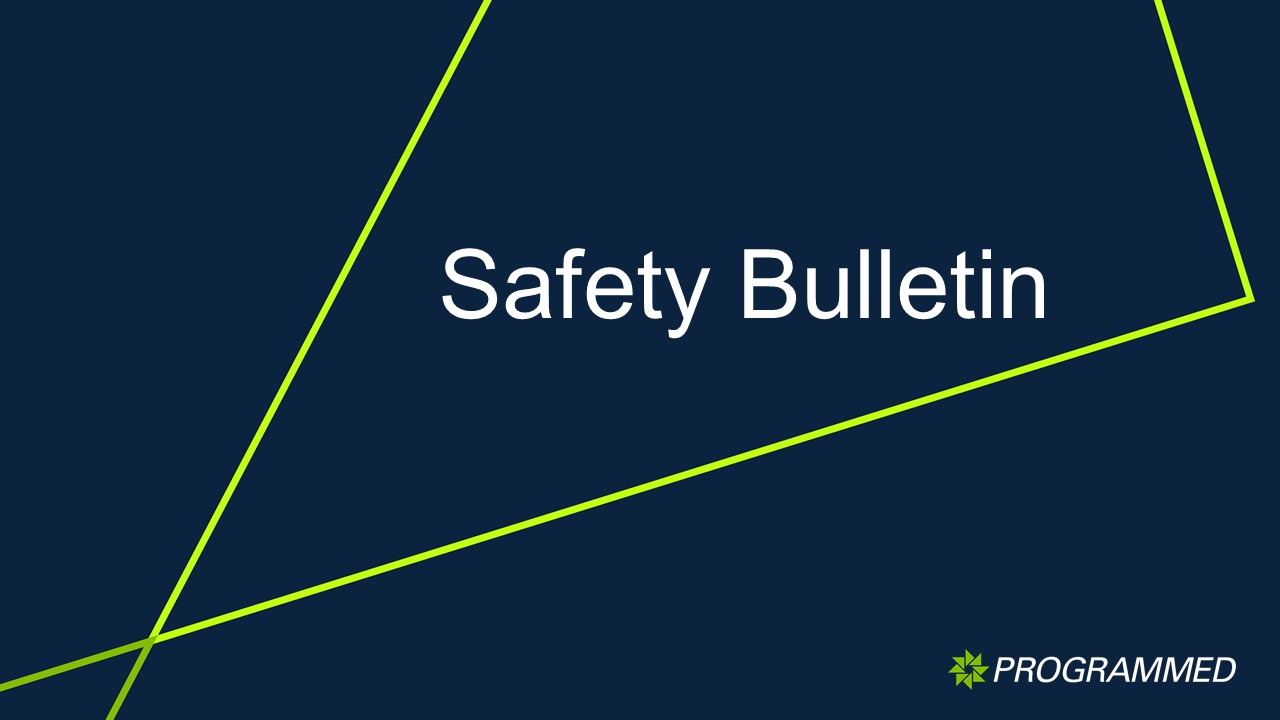
Background
Crystalline silica is a natural mineral found in many materials such as engineered stone, granite, sandstone, concrete, bricks, tiles, and mortar. Respirable crystalline silica dust is a hazardous substance which can lead to serious health effects if it is inhaled.
The Occupational Health and Safety Regulations 2017 (OHS Regulations) have been amended to provide greater protection to Victorian employees working with respirable crystalline silica. These updated regulations are being rolled out in stages with the first stage commencing on the 15th of November 2021.This included a licencing regime for engineered stone, prohibition on uncontrolled dry-cutting of engineered stone and additional regulatory oversight of high-risk crystalline silica work.
The next stage of changes came into effect on the 15th of May 2022 and businesses working with silica must now identify and document high-risk crystalline silica work and the risk control measures they have in place.
You are now required to do the following:
Identify high-risk crystalline silica work:
Before the commencement of work, you can complete a risk assessment to identify whether the crystalline silica process(s) that you perform are high-risk. Alternatively, you can choose to identify these processes as high-risk crystalline silica work without undertaking the risk assessment process.
Where completed, the risk assessment must consider:
- the specific tasks or processes;
- the form of crystalline silica to be used;
- the proportion of crystalline silica in the material;
- previous atmospheric monitoring results;
- the likely frequency and duration of exposure to crystalline silica dust;
- any information about incidents, illnesses or diseases associated with exposure to crystalline silica dust at the workplace.
High Risk Crystalline Work & Processes
What is high risk crystalline silica work?
High risk crystalline silica work is work performed in connection with a crystalline silica process that is reasonably likely to result in:
- an airborne concentration of respirable crystalline silica that exceeds half the exposure standard for respirable crystalline silica, or
- a risk to the health of a person at the workplace.
Note: The workplace exposure standard for respirable crystalline silica (silica dust) that must not be exceeded is 0.05 mg/m3 (eight-hour time weighted average).
What is a crystalline silica process?
A crystalline silica process means one or more of the following processes carried out at a workplace:
- the use of a power tool or other form of mechanical plant to cut, grind, polish, or crush material containing crystalline silica or to carry out any other activity involving material containing crystalline silica that generates crystalline silica dust
- the use of a roadheader on an excavated face if the material in the face contains crystalline silica
- a process that exposes a person to crystalline silica dust arising from the manufacture or handling of material that contains crystalline silica
- the mechanical screening of crushed material containing crystalline silica
- a quarrying process involving material containing crystalline silica
- a tunnelling process involving material containing crystalline silica
- a process determined by WorkSafe to be a crystalline silica process.
Record high-risk crystalline silica work:
If a risk assessment is completed, a written document is required outlining how the matters listed were taken into account and whether or not the process(s) are high risk. The record must be kept for the period during which the process(s) was undertaken at the workplace. This record must be made accessible to any employee who may be exposed to crystalline silica dust.
Develop a crystalline silica hazard control statement (CSHCS):
Before commencing high-risk crystalline silica work (HRCSW), a crystalline silica hazard control statement (CSHCS) must be prepared and the work must be performed in accordance with the CSHCS.
If the task being completed is high risk construction work and a Safe Work Method Statement (SWMS) has been prepared that outlines the matters required within a CSHCS, then a separate CSHCS is not needed. The SWMS must be specific to the task being carried out and address the associated hazards and controls.
A CSHCS template and guidance to complete can be accessed here
What needs to be included in a hazard control statement?
The hazard control statement must:
- state the hazards and risks to health associated with the HRCSW
- clearly detail the measures selected to control those risks in accordance with the hierarchy of controls
- describe how the risk control measures will be implemented
- if an analysis is required of samples, contain the results of that analysis
- be set out and expressed in a way that is readily accessible and comprehensible to the persons who use it.
The hazard control statement should also identify the:
- date and location the HRCSW is to be performed
- person(s) responsible for ensuring selected risk controls are implemented and maintained
- names of workers consulted in the document’s preparation.
HSE Representative: Leanne Owen
Date of Issue: 4 July 2022